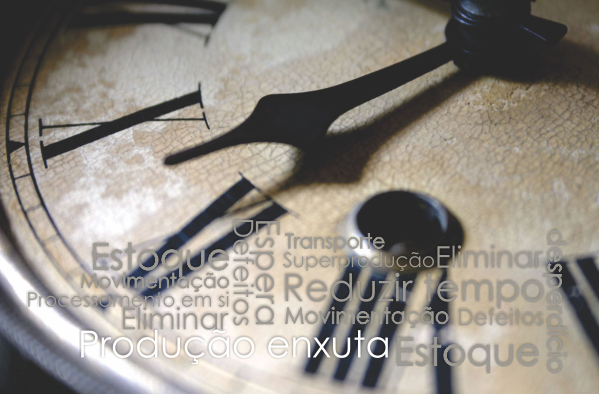
Lean Manufacturing: como funciona?
A metodologia Lean Manufacturing, ou a cultura de produção enxuta, é uma filosofia de gestão, que visa à eficiência dos processos. Isso se dá a partir da otimização do tempo e da eliminação de desperdícios.
Assim, busca atingir um sistema produtivo melhor, mais enxuto, barato e ágil, através da identificação e posterior eliminação das perdas.
O Lean Manufacturing potencializa a busca da competitividade, sendo a sua aplicação possível em todos os setores da empresa e independente do número de funcionários,
Por isso, ao longo das últimas décadas, organizações de praticamente todos os setores têm usado o Lean para transformar algumas realidades gerenciais, potencializando resultados e ampliando a capacidade dos recursos humanos.
Nesse sentido, o sucesso da implantação do Lean Manufacturing pressupõe pré-requisitos de liderança, além de mudança cultural profunda e abrangente, contribuindo para uma gestão eficaz.
_____________________________________________________________
Leia também o artigo sobre A importância da metodologia Lean
_____________________________________________________________
Detectar os oito desperdícios
A prática do Lean Manufacturing consiste em identificar as atividades que agregam valor e eliminar, ou pelo menos reduzir, os desperdícios.
Dessa forma, a gestão tem como um de seus pilares o gerenciamento diário, tornando a melhoria contínua uma atividade rotineira dentro da organização.
Assim, eliminando continuamente os desperdícios, é possível aumentar o nível de competitividade no mercado.
Por isso, atente-se aos oito desperdícios para os quais o Lean Manufacturing alerta:
1 – Defeitos e retrabalho
Refazer o que já foi feito, em geral, implica em novos investimentos, recursos, matéria-prima, logística de transporte etc. O retrabalho acaba aumentando os custos da produção.
O ideal, portanto, é focar no controle de qualidade, evitando as falhas.
2 – Excesso de produção
Para evitar o excesso de produção, a organização deve estudar os processos e fluxos de trabalho. Além disso, deve mensurar o quanto cada atividade influencia no resultado final.
3 – Processamento impróprio
São os defeitos ou limitações que afetam o processamento. Nesse sentido, a produção pode parar ou passa a se desenvolver de forma muito lenta.
De acordo com o Lean Manufacturing, para evitar este tipo de desperdício, é preciso investir em manutenção e garantir que a equipe possua equipamentos corretos para o desenvolvimento de suas atividades.
4 – Movimentos desnecessários
É o desperdício que ocorre com o trânsito de pessoas que não precisaria existir.
Acontece quando o colaborador precisa se movimentar para concluir etapas do desenvolvimento, por exemplo, em outro prédio da corporação.
Por isso, é preciso repensar as estratégias, evitando deslocamentos desnecessários.
5 – Transporte
Acontece quando é preciso mover produtos ou pessoas entre localidades.
O correto, portanto, é que o transporte aconteça em uma única direção, a caminho do cliente final.
Para que não haja nenhum tipo de movimentação desnecessária, o Lean Manufacturing recomenda investir em logística. Isso evita traçar rotas conflitantes entre os setores ou linhas de produção.
6 – Excesso de estoque
Ao produzir produtos que vão além da capacidade de venda imediata, é preciso considerar o espaço para armazenamento.
O estoque em excesso, por sua vez, pode ser danificado, se tornar obsoleto ou ultrapassar o prazo de validade, dependendo do que será comercializado.
Para a filosofia Lean, portanto, o ideal é evitar estoque além da demanda, tanto do produto final, quanto de matéria-prima, já que os efeitos danosos ao processo são os mesmos.
Dessa maneira, com estoque reduzido, é muito mais fácil resolver e reparar possíveis danos.
7 – Intelectual (pessoas)
É o desperdício de capital humano. Ele acontece quando o colaborador exerce funções aquém da sua capacidade.
Este tipo de desperdício não é tão perceptível quanto os outros, mas afeta intimamente a produtividade e a qualidade final da produção.
8 – Espera
É o tempo de espera, que o cliente final não enxerga como valor. Dessa forma, eliminar o tempo de espera, que não agrega valor, é possível quando não há ruídos na comunicação interna.
Sincronizar tarefas e colocar em prática a priorização, por exemplo, também evitam que o desperdício de tempo chegue ao consumidor final.
_____________________________________________________________
OS 8 DESPERDÍCIOS MAIS COMUNS EM EMPRESAS: SAIBA COMO EVITÁ-LOS
_____________________________________________________________
Lean Manufacturing: como funciona?
A aplicação do conceito Lean Manufacturing possibilita às empresas a redução do desperdício e o aumento da produtividade. Isso diminui, em muitos casos, o prazo de entrega de produtos, os custos operacionais e o espaço para armazenamento.
É uma jornada que passa, principalmente, pela transformação cultural da organização, onde se torna prática comum dos funcionários identificar desperdícios, reduzi-los e eliminá-los.
Na prática, é necessário:
- Estudar o cenário da empresa;
- Mensurar o maior número de dados que for possível, para que sejam identificados os problemas e processos que não geram nenhum valor para o cliente.
É através do engajamento das pessoas envolvidas no respectivo trabalho que se consegue vislumbrar oportunidades de melhoria e ganhos sustentáveis.
Nesse sentido, a implantação do conceito de Lean Manufacturing abrange todas as atividades operacionais de uma empresa e concentra, através da eliminação do desperdício e da otimização dos processos produtivos, um “caminho sem volta”.
Como afirma o vice-presidente do SINDIMETAL RS, Arno Tomasini:
“O Lean é a única forma de aumentar a competitividade das empresas, permitindo que as experiências positivas sejam compartilhadas e multiplicadas. Devemos produzir no tempo, na qualidade e na velocidade que o cliente necessita, sem desperdício de tempo, pois o Lean é melhoria contínua”.
O que é o fluxo de valor no Lean Manufacturing?
No Lean Manufacturing, o mapa do fluxo de valor é um diagrama simples de todas as etapas envolvidas. Ele pode ser desenhado em diferentes fases, revelando oportunidades de melhoria.
Assim, a finalidade de um mapa de fluxo de valor é identificar quais atividades do processo agregam ou não ao produto comercializado.
O maior recurso administrado de um líder são as pessoas. Daí vem a importância do envolvimento de todos pela jornada do Lean Manutacturing.
Por isso, funcionários, líderes e diretores devem trabalhar visando ao objetivo comum de garantir o desenvolvimento profissional e pessoal, a sustentabilidade da organização e o crescimento da economia.
A partir do olhar mais crítico sobre a rotina da empresa, é possível identificar onde estão os gargalos, as barreiras, os retrabalhos e as atividades desnecessárias. Afinal de contas, são esses os elementos que representam custos e gastos de tempo e de espaço, mas que não agregam valor ao cliente.
__________________________________________________________________________
Saiba o que é Mapeamento do fluxo de valor (MFV)?
Artigo Relacionado – A essência da ferramenta Mapeamento do Fluxo de Valor. Autor: José Roberto Ferro – Lean Institute Brasil. Leia aqui o artigo completo.
__________________________________________________________________________
Como e onde surgiu o Lean Manufacturing?
O Sistema de Produção Lean Manufacturing, ou Produção Enxuta, nasceu no Japão, na década de 1950, após a Segunda Guerra Mundial.
A preocupação era adotar uma filosofia que eliminasse qualquer gasto desnecessário, justamente por conta da falta de recursos no período pós-guerra.
Nesta época, a indústria japonesa tinha uma produtividade muito baixa e uma enorme falta de recursos. Essa realidade, naturalmente, a impedia de adotar o modelo da Produção em massa.
A criação do sistema, por sua vez, se deve a três pessoas: o fundador da Toyota e mestre de invenções, Toyoda Sakichi; seu filho Toyoda Kiichiro e o principal executivo, o engenheiro Taiichi Ohno.
O sistema objetiva aumentar a eficiência da produção pela eliminação contínua de desperdícios.
Praticamente, o Sistema Toyota de Produção teve como alicerce o método Just in time, o Kanban e o Kaizen:
- – O Just in time tem como princípio o estoque mínimo possível;
- – O Kanban é um sistema de informação, que controla a quantidade de produção em todos os processos, sempre indicando o que produzir, quando e quanto;
- – Kaizen, por sua vez, é um meio de melhoria contínua. Para o Kaizen, sempre é possível melhorar, tanto na estrutura, quanto no indivíduo.
O Sistema Toyota de Produção vem sendo implantado em várias empresas no mundo todo. Para sua própria sobrevivência, a Toyota concebeu uma forma diferente de produzir.
Estes conceitos, desenvolvidos naquela época, norteiam até hoje o sistema, que é amplamente difundido em empresas de quaisquer outros segmentos.
Compartilhe nas redes sociais!
- Postado em: 25 junho de 2019